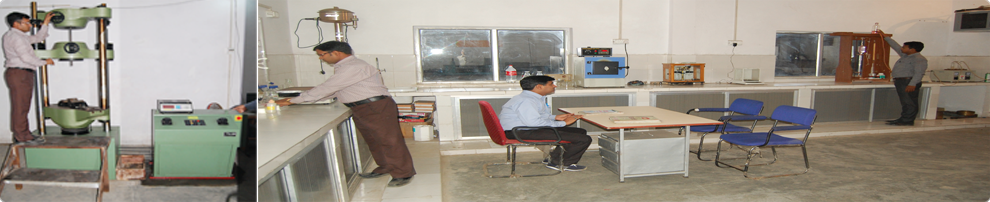
Scrap Melting and Billet casting stage --
Good quality of scrap is purchased, mainly from overseas market for ensuring best quality at Raw material stage itself.
Procurement of Best quality additives like Sponge and other chemicals viz. Silico Manganese, Ferro silicon etc. from very reputed manufacturers for better quality and composition of molten metal during melting stage.
Reduction of excessive Phosphorous and Sulphur through LRF , if present.
Induction Furnace with an efficient design features for controlling the Current and Voltage by maintaining the near about unity Power Factor, for an excellent Scrap melting with an assured homogeneous metal composition.
Chemical composition of liquid metal is continuously monitored by using Spectrometer for ensuring greater homogeneity and cohesiveness.
TMT Bars Rolling Stage
- Chemical test for re-confirmation of the right composition.
- Geometrical test such as straightness, diameter and Rib pitch etc
- Physical test such as bending and re-bending, elongation, tensile and overall strength.
- Continuous monitoring of unit weight of the bar.
- Overall control on quality assurance reports for every batch and every day’s production.
- Perfect communication system at inter departmental and intradepartmental level for having the greater control and smooth flow of information.
- See and shoot philosophy on problems arises at any level.
- Follow strictly the BIS (ISI) and International norms to maintain the quality of the product.
PRODUCT RANGE | ||||
WAVE TMT Fe-500( Fe-500, Fe-550 grades) in the range of 8mm,10mm,12mm,16mm,20mm & 25mm,28mm,32mm. | ||||
Number & weight per mtr of saria as above( Section weight) | ||||
Dia( mm) | No.of saria | Weight (per mtr) As per ISI-1786 |
Weight (per mtr) Wave TMT |
Approx. Length (Mtr/MT) |
8 | 19 | 0.367 - 0.423 | 0.371 - 0.390 | 2,500 |
10 | 13 | 0.574 - 0.660 | 0.580 - 0.600 | 1,600 |
12 | 9 | 0.844 - 0.932 | 0.852 - 0.865 | 1,100 |
16 | 5 | 1.499 - 1.657 | 1.515 - 1.535 | 630 |
20 | 3 | 2.392 - 2.540 | 2.408 - 2.420 | 400 |
25 | 1 | 3.739 - 3.970 | 3.754 - 3.773 | 260 |
28 | 1 | 4.685-4.975 | 4.685-4.830 | 207 |
32 | 1 | 6.121-6.499 | 6.120-6.450 | 158 |
Chemical Properties | ||||
DESCRIPTION | IS 1786 : 2008 |
Wave TMT | ||
Fe-500 | Fe-550 | Fe-500 | Fe-550 | |
Carbon (% max) | 0.300 | 0.300 | 0.260 | 0.250 |
Sulphur (%max) | 0.055 | 0.055 | 0.045 | 0.040 |
Phosphorus (%max) | 0.055 | 0.050 | 0.045 | 0.045 |
Sulphur + Phosphorus (% max) | 0.105 | 0.100 | 0.090 | 0.085 |
Physical Properties | ||||
DESCRIPTION | IS 1786 : 2008 | Wave TMT | ||
Fe-500 | Fe-550 | Fe-500 | Fe-550 | |
0.2% Proof Stress Min (N/mm2) | 500.0 | 550.0 | 550.0 | 580.0 |
Tensile Strength Min (N/mm2) | 545.0 | 585.0 | 560.0 | 600.0 |
% Elongation,Min. | 12.00 | 10.00 | 18.00 | 17.50 |